ハンダなどの接着材料を使う代わりに、超音波を使って電極を基板へ接合する。それが「電極接合装置(TMBBM)」です。接着材料を使わないため、製造コストを削減できます。環境への負荷も低減します。割れやすいガラス基板に対する、直接接合も実現しました。
特長
独自の超音波接合を応用し、ガラス基板にアルミ電極を直接接合
割れやすいガラス基板に対しての超音波接合を実現したことで様々な用途への適用の可能性が広がりました。
接着材料が不要、製造コストを大幅に削減、環境負荷低減にも大きく寄与
電極と基板を直接接合する為、間接材料は一切使用していません。
希少金属も使用しない為、環境負荷低減にも寄与します。
直接接合により接触抵抗を低減、接合安定性を向上
間接材料を使用しない為、接触抵抗を低減します。また、接合安定性も向上する為、生産性・品質向上に寄与します。
基板、下地層への熱ダメージのない常温接合プロセス
熱エネルギーによる接合ではない為、基板や下地層への熱ダメージはなく、品質向上に寄与します。
接合事例
- 基板接合面材質
Mo, Ag, Ti, Al, Ni, Cr, ITO, ZnO, etc. - 基板ガラス厚さ
0.6mm to 4.0mm
接合原理
原子間引力による直接接合
素材表面に圧力と超音波振動を与えることで、表面酸化皮膜を除去します。
更に、接合界面の金属が塑性流動し、原子同士が相互に引力を及ぼす距離まで接近することで接合します。
製造コスト削減効果(太陽光パネル製造装置)
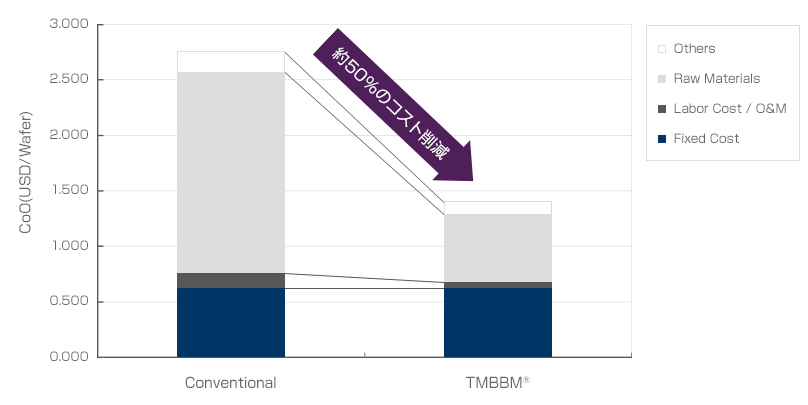
ハンダ材料・ペースト等の接着材料費がゼロ
接合材料コストを大幅低減することが出来ます。
予備ハンダ・フラックス不要で省スペース
装置コスト低減に寄与します。
装置外観・動作 (太陽光パネル製造装置)
大型基板向けの量産機です。
(対象基板サイズ:650×1650、タクトタイム:50秒/枚)